When it comes to metal cans, you might wonder, “What exactly is the difference between two-piece and three-piece cans? Are you familiar with their structure and uses?” Two-piece cans consist of a single metal sheet shaped into a body with an attached bottom and a separate lid. In contrast, three-piece cans include three parts: a cylindrical body, a bottom, and a top, joined together.
Two-piece cans often package beverages due to their seamless design, while three-piece cans are versatile in size and shape, making them ideal for food and industrial products. Each type has unique advantages depending on your needs.
Key Takeaways
- Two-piece cans use one metal sheet. They are light and strong, great for drinks.
- Three-piece cans have three parts. They can be made in different sizes and shapes, good for food and industrial items.
- Two-piece cans seal well. They stop leaks and keep drinks fresh, perfect for soda.
- Three-piece cans cost less to make for small batches. They are flexible in design.
- Use two-piece cans for big production. They save materials and work faster.
- Three-piece cans work for many uses, like special foods or industrial packaging. Their design can be changed easily.
- Both types have good points. Pick based on your product’s needs, like cost, strength, or recycling.
- Two-piece cans help the planet. Aluminum can be recycled fully and lowers harm to nature.
What exactly is the difference between two-piece and three-piece cans? Are you familiar with their structure and uses?
What Are Two-Piece Cans?
Design and Structure
Two-piece cans consist of a single metal sheet that forms the body and bottom as one seamless unit. This design eliminates the need for side seams, making the can lightweight and highly durable. The lid is a separate component, attached after the can is filled. The seamless structure ensures excellent sealing, which is crucial for preserving the contents’ freshness and quality.
Common Materials Used
Two-piece cans are typically made from aluminum or steel. Aluminum is the preferred choice for beverage cans due to its lightweight nature and resistance to corrosion. Steel, often coated with a protective layer, is used for food packaging, offering strength and durability. The material choice depends on the intended application, ensuring the can meets specific requirements for safety and performance.
What Are Three-Piece Cans?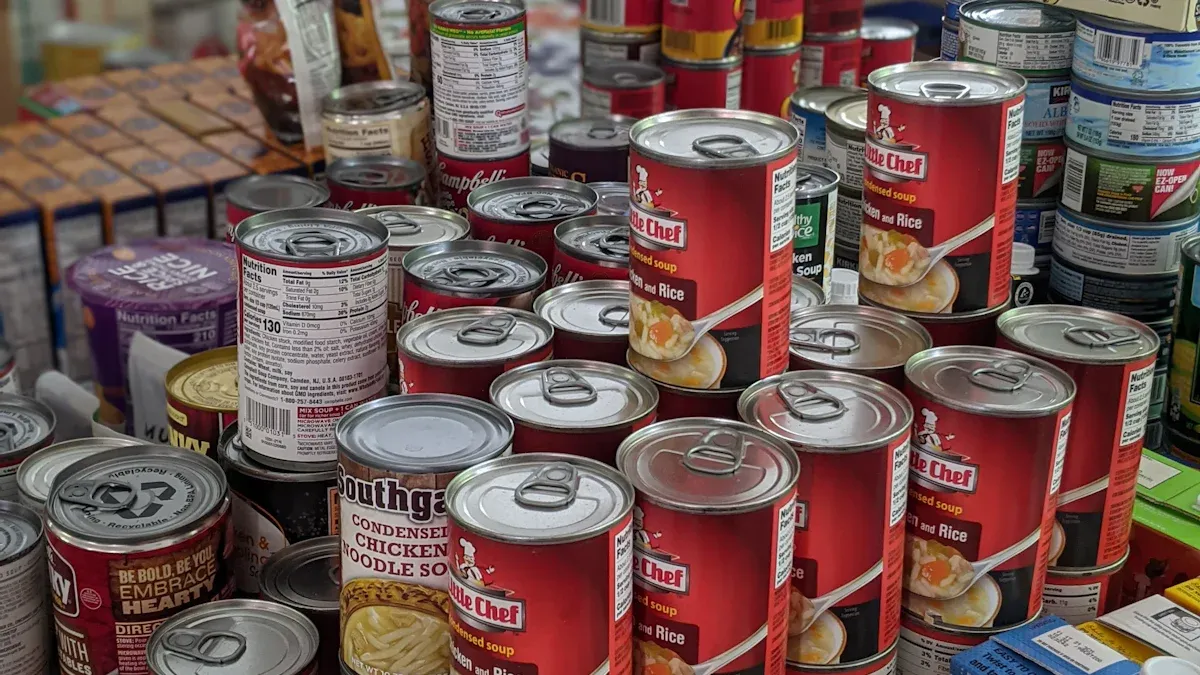
Design and Structure
Three-piece cans are constructed from three distinct components: a cylindrical body, a top, and a bottom. The body is formed by rolling a flat sheet of tinplate metal into a cylinder and sealing the edges using welding or soldering. The top and bottom are then attached to the body, creating a complete can. This design allows for greater flexibility in size and shape, making it suitable for a wide range of applications.
Common Materials Used
Three-piece cans are commonly made from tinplate or tin-free steel. These materials provide the necessary rigidity and are often coated to prevent corrosion. The use of tinplate ensures the can is safe for food storage, while the flexibility of the material allows for customization in design and size.
Key Differences Between Two-Piece and Three-Piece Cans
Manufacturing Process
The manufacturing process for two-piece cans involves a deep-drawing technique, where a single sheet of metal is stretched and shaped into the desired form. This process is efficient and reduces material waste. In contrast, three-piece cans require multiple steps, including rolling, welding, and attaching the ends. While this process is more complex, it offers greater versatility in terms of size and shape.
Application Field | Type of Can | Key Characteristics |
---|---|---|
Drinks | 2-piece | Dominates the market with DWI technology. |
Industrial | 3-piece | Versatile for various uses and effective at low production speeds. |
Food | 3-piece and 2-piece | Offers different solutions with advantages and disadvantages in design and destruction processes. |
Sealing and Durability
Two-piece cans excel in sealing due to their seamless design. This feature minimizes the risk of leaks and ensures the contents remain fresh. Three-piece cans, however, rely on welded seams, which may pose a higher risk of leakage if not properly sealed. Despite this, three-piece cans are robust and can withstand various handling conditions, making them suitable for industrial applications.
Cost Implications
Two-piece cans are cost-effective for large-scale production due to their streamlined manufacturing process. They also use up to 15% less material compared to three-piece cans, reducing overall costs. However, the initial investment in equipment for two-piece can production is higher. Three-piece cans, on the other hand, are more economical for smaller production runs and offer flexibility in design, which can offset the higher material usage.
Tip: If you prioritize cost efficiency for bulk production, two-piece cans are ideal. For smaller, customized batches, three-piece cans provide better value.
Advantages and Disadvantages of Two-Piece and Three-Piece Cans
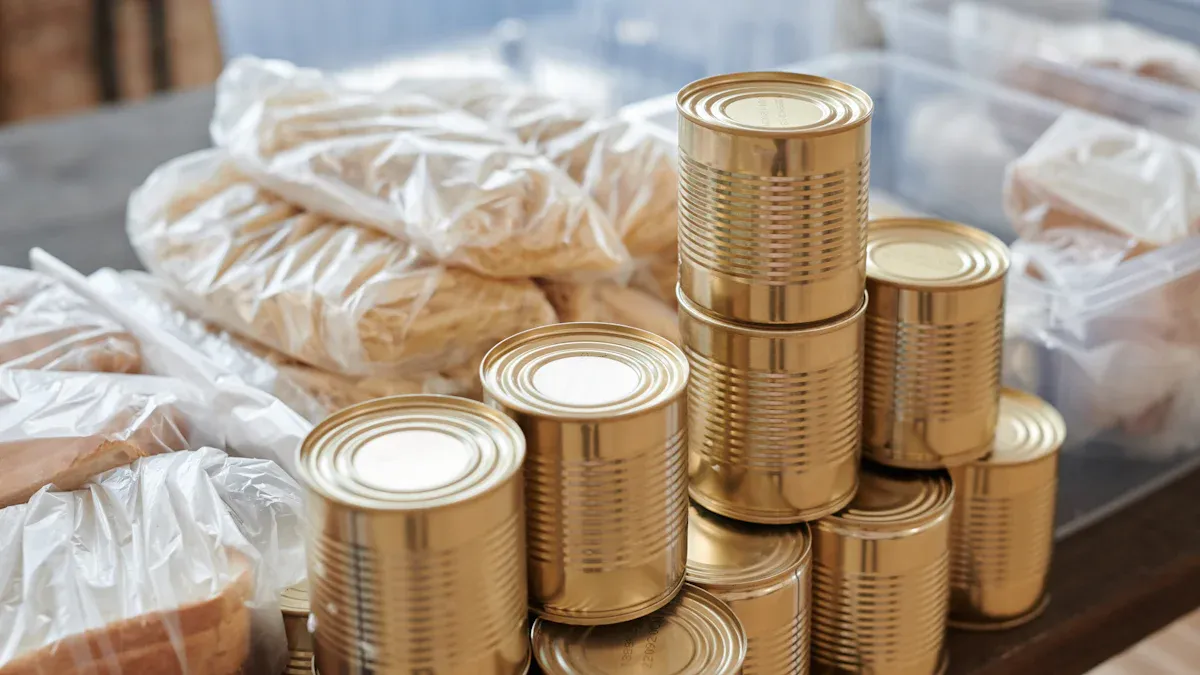
Advantages of Two-Piece Cans
Lightweight and Seamless Design
Two-piece cans stand out for their lightweight and seamless construction. The absence of side seams reduces the risk of leaks, ensuring the contents remain secure and fresh. This design also makes the cans easier to handle and transport, which is especially beneficial for industries requiring high-speed production. The seamless structure enhances durability, making these cans ideal for carbonated beverages that need to withstand internal pressure.
- Two-piece cans use up to 15% less material compared to three-piece cans, contributing to their lightweight nature.
- Their streamlined design simplifies the manufacturing process, improving production efficiency and reducing waste.
Ideal for Beverages
The beverage industry heavily relies on two-piece cans due to their superior sealing capabilities and aesthetic appeal. The smooth surface allows for high-quality printing, which enhances brand visibility. Additionally, the cans’ lightweight nature reduces shipping costs, making them a cost-effective choice for large-scale beverage production.
- In Southeast Asia, two-piece aluminum cans have gained popularity for ready-to-drink coffee, aligning with premiumization trends.
- The durability and recyclability of two-piece cans make them a sustainable option for the beverage sector.
Disadvantages of Two-Piece Cans
Limited Size Options
Two-piece cans face limitations in size and shape due to the deep-drawing manufacturing process. This restriction makes them less suitable for products requiring larger or uniquely shaped containers. For industries needing diverse packaging solutions, this can be a significant drawback.
- The design constraints of two-piece cans limit their application in markets like industrial packaging, where flexibility in size is crucial.
- Regional preferences, such as the demand for affordable single-serve beverages in Asia, further highlight the limitations of two-piece cans in meeting diverse consumer needs.
Higher Production Costs for Certain Applications
While two-piece cans are cost-effective for high-volume production, their initial setup costs can be prohibitive. The advanced machinery required for their manufacturing demands a significant investment, which may not be feasible for smaller producers.
- The dependency on specialized equipment increases production costs for low-volume applications.
- Innovations in can design, such as enhancing barrier properties, can further raise production expenses.
Advantages of Three-Piece Cans
Versatility in Size and Shape
Three-piece cans offer unmatched flexibility in size and shape, making them suitable for a wide range of applications. Their design allows for easy customization, catering to specific product requirements. This versatility is particularly advantageous for food and industrial packaging.
- The ability to produce cans in various sizes and shapes makes three-piece cans ideal for products like soups, sauces, and industrial chemicals.
- The use of tinplate or tin-free steel ensures the cans are robust and safe for food storage.
Cost-Effective for Bulk Production
For smaller production runs or products requiring unique designs, three-piece cans provide a cost-effective solution. Their manufacturing process, though more complex, allows for greater material utilization and design flexibility.
- Three-piece cans are less dependent on specialized equipment, reducing initial setup costs.
- Logistical vulnerabilities, such as material dependencies, are less pronounced in three-piece can production, making them a reliable choice for certain markets.
Note: If your product requires a custom size or shape, three-piece cans offer the flexibility you need without compromising on quality.
Disadvantages of Three-Piece Cans
Potential for Leakage at Seams
Three-piece cans rely on seams to join the body, top, and bottom. These seams can become weak points, especially if the sealing process is not precise. You might notice this issue more in products that require long-term storage or are exposed to extreme conditions.
- Why does this happen? The seams are created through welding or soldering, which can sometimes leave small gaps or imperfections. Over time, these gaps may allow air or liquid to escape, compromising the product’s quality.
- What does it mean for you? If you need packaging for carbonated beverages or highly perishable goods, this risk could lead to spoilage or reduced shelf life.
Tip: Always ensure your supplier uses advanced sealing techniques to minimize the risk of leakage. High-quality manufacturing processes can significantly reduce this issue.
Heavier Compared to Two-Piece Cans
Three-piece cans tend to weigh more than their two-piece counterparts. This added weight comes from the thicker materials used and the additional components required for assembly.
- How does this affect you? Heavier cans increase transportation costs, especially for bulk shipments. If you are in the beverage or food industry, this could impact your overall logistics budget.
- Why does weight matter? Consumers often prefer lightweight packaging for convenience. Heavier cans might feel less user-friendly, especially for single-serve products.
Feature | Two-Piece Cans | Three-Piece Cans |
---|---|---|
Weight | Lightweight | Heavier |
Consumer Preference | High | Moderate |
Transportation Costs | Lower | Higher |
Note: If your product requires frequent shipping or targets a market that values portability, the weight of three-piece cans could be a disadvantage.
By understanding these drawbacks, you can make informed decisions about whether three-piece cans align with your product’s needs and your business goals.
Applications in Different Industries
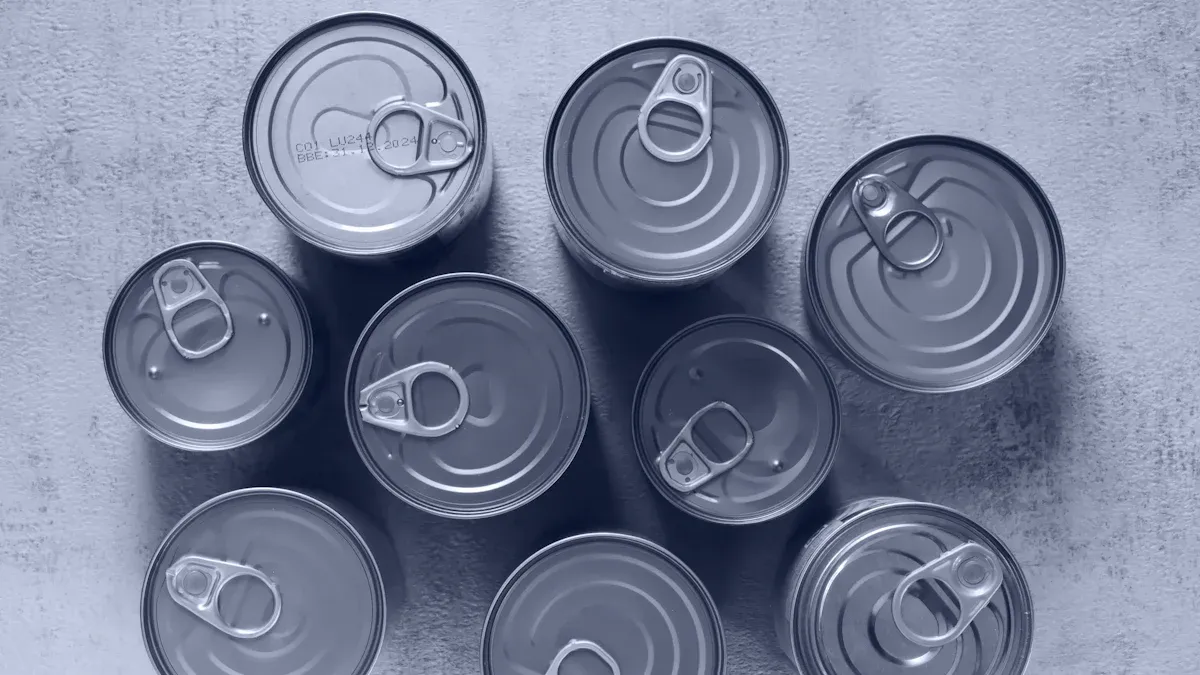
Food Industry
Suitability of Two-Piece Cans
Two-piece cans excel in the food industry when it comes to packaging efficiency and product preservation. Their seamless design ensures airtight sealing, which is essential for maintaining the freshness and safety of food products. These cans are particularly suitable for ready-to-eat meals, soups, and beverages that require high-pressure sealing. The lightweight nature of two-piece cans also reduces transportation costs, making them a cost-effective choice for large-scale food production.
The growing demand for convenience foods has further boosted the use of two-piece cans. For instance, the ready-to-eat meals segment is projected to grow at a compound annual growth rate (CAGR) of over 6% between 2025 and 2034. This trend highlights the increasing reliance on efficient and durable packaging solutions like two-piece cans.
Suitability of Three-Piece Cans
Three-piece cans offer unmatched versatility in the food industry. Their ability to accommodate various sizes and shapes makes them ideal for packaging a wide range of products, from canned vegetables to sauces and even bulk food items. The use of tinplate or tin-free steel ensures these cans are robust and safe for food storage.
In addition to their flexibility, three-piece cans are well-suited for smaller production runs. This makes them a preferred choice for niche food products or limited-edition packaging. The North American market, which holds over 35% of the global food cans market share, has seen significant adoption of three-piece cans due to their adaptability and cost-effectiveness.
Aspect | Details |
---|---|
Market Growth | The food cans market is projected to grow significantly, with aluminum cans expected to reach over USD 20 billion by 2034. |
Fastest Growing Segment | Ready-to-eat meals segment with a CAGR of over 6% between 2025 and 2034. |
North America Market Share | Over 35% share in 2024, driven by convenience and health-conscious consumer trends. |
Beverage Industry
Why Two-Piece Cans Dominate
Two-piece cans dominate the beverage industry due to their lightweight and seamless design. These features make them ideal for carbonated drinks, juices, and energy beverages. The seamless structure ensures excellent sealing, which is crucial for maintaining carbonation and freshness. Additionally, the smooth surface of two-piece cans allows for high-quality printing, enhancing brand visibility.
The beverage industry has also embraced two-piece aluminum cans for their sustainability. Aluminum is 100% recyclable, making it an eco-friendly choice that aligns with consumer preferences for sustainable packaging. This has contributed to the rapid growth of aluminum cans, which are expected to reach over USD 20 billion by 2034.
Challenges with Three-Piece Cans
Three-piece cans face challenges in the beverage industry due to their heavier weight and potential for leakage at seams. These factors make them less suitable for carbonated drinks, where maintaining internal pressure is critical. Additionally, the higher material usage in three-piece cans increases production costs, making them less competitive in a market dominated by two-piece cans.
However, three-piece cans still find limited use in the beverage industry for non-carbonated drinks or specialty products that require unique packaging designs. Their ability to accommodate custom shapes and sizes offers a niche advantage in certain segments.
Industrial and Non-Food Applications
Benefits of Three-Piece Cans
Three-piece cans shine in industrial and non-food applications due to their durability and versatility. Their robust construction makes them suitable for packaging chemicals, paints, and other industrial products that require secure and reliable containment. The ability to produce cans in various sizes and shapes further enhances their utility in this sector.
The use of tinplate or tin-free steel in three-piece cans ensures they can withstand harsh conditions, such as exposure to chemicals or extreme temperatures. This makes them a preferred choice for industrial packaging solutions.
Limitations of Two-Piece Cans
Two-piece cans face limitations in industrial applications due to their restricted size and shape options. The deep-drawing manufacturing process used for two-piece cans limits their ability to accommodate larger or uniquely shaped products. Additionally, the thinner walls of two-piece cans may not provide the necessary strength for industrial use.
For bulk handling and storage, three-piece cans offer a more practical solution. Their ability to group primary packages into secondary or tertiary packaging types ensures easier handling and transportation, making them a reliable choice for industrial needs.
Packaging Type | Description |
---|---|
Primary | Direct contact with food, essential for protection and preservation. |
Secondary | Grouping of primary packages for easier handling. |
Tertiary | Bulk handling packaging solutions. |
Tip: For industrial applications, consider three-piece cans for their strength and adaptability. They provide a reliable solution for packaging products that require durability and customization.
Perspectives from Manufacturers and Packers
Ease of Use and Production Efficiency
Two-Piece Cans in High-Speed Production
Two-piece cans excel in high-speed production environments. Their streamlined manufacturing process, known as “Drawn and Ironed,” allows for rapid production with minimal material waste. This efficiency makes them a top choice for industries requiring large-scale output, such as the beverage sector. You’ll find that their lightweight design simplifies handling during production and transportation, further enhancing operational efficiency.
Advances in engineering have also improved the durability and sustainability of two-piece cans. Energy-efficient machinery now supports faster production speeds while reducing the carbon footprint. Digital technologies, like automation and quality control systems, ensure consistent results, minimizing defects and downtime.
Can Type | Manufacturing Process | Advantages |
---|---|---|
Two-piece Cans | Drawn & Ironed | Lightweight, efficient production |
Three-piece Cans | Drawn & Redrawn, Impact Extrusion | Versatile design, cost-effective |
Flexibility of Three-Piece Cans
Three-piece cans offer unmatched flexibility in design and size. Their “Drawn and Redrawn” or “Impact Extrusion” processes allow manufacturers to create cans in various shapes and dimensions. This versatility makes them ideal for packaging products that require unique or customized containers, such as industrial chemicals or specialty food items.
You’ll appreciate how three-piece cans adapt to smaller production runs. Unlike two-piece cans, they don’t rely on specialized equipment, which reduces setup costs. This adaptability ensures that manufacturers can meet diverse market demands without compromising efficiency. Additionally, the use of advanced materials and coatings enhances their durability, making them suitable for challenging storage conditions.
- Digital technologies improve tracking and automation during production.
- Energy-efficient machinery supports large-scale distribution while lowering environmental impact.
Recyclability and Environmental Impact
Sustainability of Two-Piece Cans
Two-piece cans lead the way in sustainability. Aluminum, the primary material used, is 100% recyclable. Recycling aluminum requires 95% less energy than producing it from raw materials, significantly reducing environmental impact. If you prioritize eco-friendly packaging, two-piece cans align with your goals.
The seamless design of two-piece cans also minimizes material usage. This reduction not only lowers production costs but also contributes to sustainability by conserving resources. Manufacturers increasingly adopt energy-efficient machinery, further enhancing the environmental benefits of two-piece cans.
Recycling Challenges with Three-Piece Cans
Three-piece cans face more challenges in recycling. Their construction involves multiple materials, such as tinplate and coatings, which complicate the recycling process. Separating these components requires additional steps, increasing energy consumption and costs.
Despite these challenges, three-piece cans remain a viable option for industries prioritizing durability and customization. Advances in material sciences aim to improve their recyclability. For example, newer coatings reduce contamination risks, making the recycling process more efficient. If you need packaging for industrial or niche products, three-piece cans still offer a practical solution.
Cost-Effectiveness
Cost Comparison for Small-Scale Production
For small-scale production, three-piece cans provide a cost-effective solution. Their manufacturing process doesn’t require specialized equipment, reducing initial investment costs. You can easily customize these cans to meet specific needs, making them ideal for limited-edition products or niche markets.
Two-piece cans, on the other hand, involve higher setup costs due to the advanced machinery required. While they excel in high-volume production, their cost-effectiveness diminishes for smaller batches. If your focus is on flexibility and affordability for smaller runs, three-piece cans are the better choice.
Cost Comparison for Large-Scale Production
In large-scale production, two-piece cans outperform three-piece cans in cost efficiency. Their streamlined manufacturing process uses up to 15% less material, reducing overall expenses. High-speed production lines further enhance their economic advantage, making them the preferred choice for industries like beverages.
Three-piece cans, while versatile, incur higher material costs due to their multi-component design. Their slower production speeds also make them less competitive for large-scale operations. If your goal is to maximize efficiency and minimize costs for bulk production, two-piece cans offer the best value.
Tip: Consider your production scale and packaging needs when choosing between two-piece and three-piece cans. Each type offers unique advantages depending on your priorities.
Choosing between two-piece and three-piece cans depends on your specific needs. Two-piece cans excel in cost-effectiveness, ecological benefits, and consumer appeal, especially in the beverage industry. Their seamless design ensures better shelf life and branding opportunities. On the other hand, three-piece cans offer unmatched versatility in size and shape, making them ideal for industrial and niche food applications.
Feature | Two-Piece Cans | Three-Piece Cans |
---|---|---|
Cost-Effectiveness | Lower production costs due to less material used | Higher production costs |
Ecological Benefits | Reduced environmental impact and carbon emissions | Greater material usage |
Consumer Preferences | Strong acceptance in the beverage industry | Less popular in comparison |
Shelf Life | Better due to oxygen and biological contaminant resistance | Varies |
Branding Opportunities | Enhanced by modern printing technologies | Limited branding options |
When deciding, consider your priorities. For beverages, two-piece cans are the best choice. For food or industrial products requiring custom sizes, three-piece cans provide flexibility. Always weigh cost, durability, and recyclability to make the most informed decision.
FAQ
What is the main difference between two-piece and three-piece cans?
Two-piece cans have a seamless body and bottom made from one metal sheet, while three-piece cans consist of a cylindrical body, top, and bottom joined by seams. This structural difference impacts their durability, weight, and manufacturing process.
Which type of can is better for beverages?
Two-piece cans are ideal for beverages. Their seamless design ensures excellent sealing, which preserves carbonation and freshness. They are also lightweight, making them easier to transport and handle in high-speed production environments.
Are three-piece cans suitable for food packaging?
Yes, three-piece cans work well for food packaging. Their customizable size and shape make them versatile for various food products, including soups, sauces, and bulk items. Tinplate material ensures safety and durability for food storage.
How do two-piece cans contribute to sustainability?
Two-piece cans, often made from aluminum, are 100% recyclable. Recycling aluminum uses 95% less energy than producing it from raw materials. Their lightweight design also reduces transportation emissions, making them an eco-friendly choice.
Can three-piece cans handle industrial applications?
Three-piece cans excel in industrial applications. Their robust construction and customizable design make them suitable for packaging chemicals, paints, and other industrial products. They withstand harsh conditions like extreme temperatures and chemical exposure.
Why are two-piece cans more cost-effective for large-scale production?
Two-piece cans use up to 15% less material and have a streamlined manufacturing process. These factors reduce production costs for high-volume operations, making them a cost-effective choice for industries like beverages.
Do three-piece cans have any limitations?
Three-piece cans may face issues like potential leakage at seams and heavier weight compared to two-piece cans. These factors can increase transportation costs and make them less suitable for carbonated beverages or lightweight packaging needs.
How do I choose between two-piece and three-piece cans?
Consider your product’s needs. For beverages or high-speed production, choose two-piece cans. For food or industrial products requiring custom sizes, three-piece cans offer flexibility. Evaluate factors like cost, durability, and recyclability to make the best decision.
Tip: Always align your choice with your product’s packaging requirements and target market preferences.